Technologia topienia
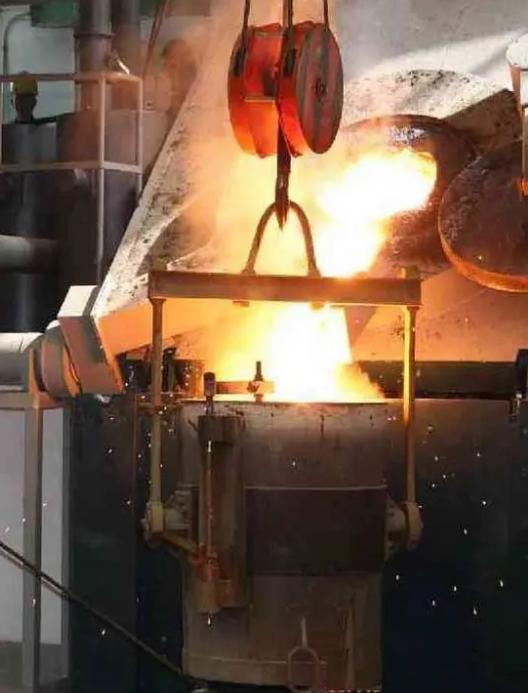
Obecnie do wytapiania produktów przetwórstwa miedzi stosuje się na ogół piec do wytapiania indukcyjnego, a także wytapianie w piecu pogłosowym i wytapianie w piecu szybowym.
Wytapianie w piecu indukcyjnym nadaje się do wszystkich rodzajów miedzi i stopów miedzi i ma właściwości czystego wytapiania i zapewnia jakość stopu.Ze względu na budowę pieca piece indukcyjne dzielą się na piece indukcyjne z rdzeniem i piece indukcyjne bez rdzenia.Piec indukcyjny z rdzeniem charakteryzuje się wysoką wydajnością produkcyjną i wysoką sprawnością cieplną i nadaje się do ciągłego topienia jednego rodzaju miedzi i stopów miedzi, takich jak miedź czerwona i mosiądz.Bezrdzeniowy piec indukcyjny charakteryzuje się dużą szybkością nagrzewania i łatwą wymianą odmian stopów.Nadaje się do topienia miedzi i stopów miedzi o wysokiej temperaturze topnienia i różnych odmian, takich jak brąz i miedzionikiel.
Próżniowy piec indukcyjny to piec indukcyjny wyposażony w system próżniowy, odpowiedni do wytapiania miedzi i stopów miedzi łatwych do wdychania i utleniania, takich jak miedź beztlenowa, brąz berylowy, brąz cyrkonowy, brąz magnezowy itp. do próżni elektrycznej.
Wytapianie w piecu pogłosowym umożliwia rafinację i usuwanie zanieczyszczeń ze stopu i jest stosowane głównie do wytapiania złomu miedzi.Piec szybowy jest rodzajem pieca do szybkiego topienia ciągłego, którego zalety to wysoka sprawność cieplna, wysoka szybkość topienia i wygodne wyłączanie pieca.Można kontrolować;nie ma procesu rafinacji, więc zdecydowana większość surowców musi być miedzią katodową.Piece szybowe są zwykle stosowane w maszynach do odlewania ciągłego do odlewania ciągłego, ale mogą być również stosowane z piecami wsporczymi do odlewania półciągłego.
Trend rozwojowy technologii produkcji wytapiania miedzi znajduje odzwierciedlenie głównie w zmniejszeniu strat przy spalaniu surowców, zmniejszeniu utleniania i wdychania wytopu, poprawie jakości wytopu i przyjęciu wysokiej wydajności (szybkość topienia pieca indukcyjnego jest większa niż 10 t/h), wielkogabarytowych (wydajność pieca indukcyjnego może być większa niż 35 t/zestaw), długiej żywotności (żywotność wyłożenia od 1 do 2 lat) i energooszczędnych (energochłonność pieca indukcyjnego piec ma moc mniejszą niż 360 kWh/t), piec podtrzymujący jest wyposażony w urządzenie odgazowujące (odgazowanie gazu CO), a piec indukcyjny. Czujnik ma strukturę natryskową, elektryczne urządzenia sterujące wykorzystują dwukierunkowy tyrystor i zasilacz z konwersją częstotliwości, wstępne podgrzewanie pieca, monitorowanie stanu pieca i pola temperatury materiału ogniotrwałego oraz system alarmowy, piec przetrzymujący jest wyposażony w urządzenie ważące, a kontrola temperatury jest dokładniejsza.
Sprzęt produkcyjny - linia do cięcia wzdłużnego
Produkcja linii do cięcia wzdłużnego taśmy miedzianej to ciągła linia produkcyjna do cięcia wzdłużnego i wzdłużnego, która poszerza szeroką cewkę poprzez rozwijarkę, przycina cewkę do wymaganej szerokości przez maszynę do cięcia wzdłużnego i przewija ją na kilka cewek przez nawijarkę. (Regał magazynowy) Do przechowywania rolek na regale użyj dźwigu
↓
(Samochód załadowczy) Za pomocą wózka podającego ręcznie nałóż rolkę materiału na bęben rozwijający i zaciśnij ją
↓
(Odwijak i rolka dociskowa zapobiegająca poluzowaniu) Odwiń zwój za pomocą prowadnicy otwierającej i rolki dociskowej
↓
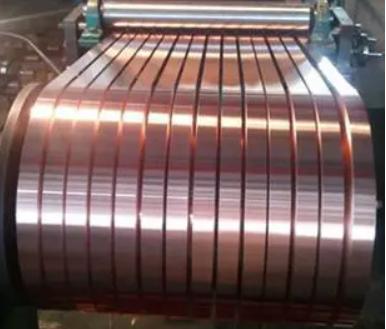
(pętla NO·1 i mostek obrotowy) magazyn i bufor
↓
(Prowadnica krawędziowa i urządzenie z rolką dociskową) Rolki pionowe prowadzą arkusz do rolek dociskowych, aby zapobiec odchyleniom. Szerokość i położenie rolek prowadzących w pionie można regulować
↓
(Maszyna do cięcia wzdłużnego) wejdź do maszyny do cięcia wzdłużnego w celu pozycjonowania i cięcia wzdłużnego
↓
(Szybka wymiana gniazda obrotowego) Wymiana grupy narzędzi
↓
(Urządzenie do nawijania złomu) Odetnij złom
↓ (stół prowadzący końca wylotowego i ogranicznik ogona cewki) Przedstaw chwytacz nr 2
↓
(mostek obrotowy i chwytacz nr 2) przechowywanie materiału i eliminacja różnicy grubości
↓
(Urządzenie do napinania płyty dociskowej i wałka rozprężającego powietrze) zapewnia siłę naciągu, separację płyty i paska
↓
(Nożyce do cięcia wzdłużnego, urządzenie do pomiaru długości skrętu i stół prowadzący) Pomiar długości, segmentacja cewki o stałej długości, prowadnica gwintowania taśmy
↓
(nawijarka, urządzenie separujące, urządzenie dociskowe) taśma separacyjna, zwijanie
↓
(rozładunek ciężarówki, pakowanie) rozładunek i pakowanie taśmy miedzianej
Technologia walcowania na gorąco
Walcowanie na gorąco stosowane jest głównie do walcowania kęsów wlewków do produkcji arkuszy, taśm i folii.
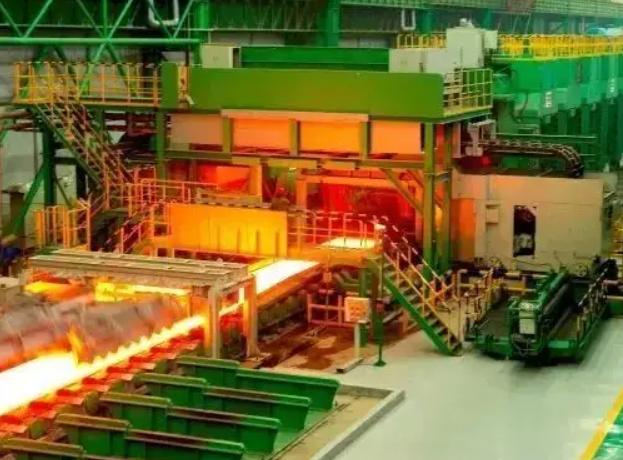
Specyfikacje wlewków do walcowania kęsów powinny uwzględniać takie czynniki, jak różnorodność produktu, skala produkcji, metoda odlewania itp. i są powiązane z warunkami sprzętu do walcowania (takimi jak otwór walca, średnica walca, dopuszczalny nacisk walcowania, moc silnika i długość samotoku). , itp. .Ogólnie rzecz biorąc, stosunek grubości wlewka do średnicy rolki wynosi 1: (3,5 ~ 7): szerokość jest zwykle równa lub kilkakrotnie większa od szerokości gotowego produktu, a szerokość i ilość przycinania powinny być odpowiednio dobrane uważany za.Generalnie szerokość płyty powinna wynosić 80% długości korpusu rolki.Długość wlewka powinna być rozsądnie rozważona zgodnie z warunkami produkcji.Ogólnie rzecz biorąc, przy założeniu, że można kontrolować końcową temperaturę walcowania na gorąco, im dłuższy wlewek, tym wyższa wydajność i wydajność produkcji.
Specyfikacje wlewków w małych i średnich zakładach przetwórstwa miedzi wynoszą zazwyczaj (60 ~ 150) mm x (220 ~ 450) mm x (2000 ~ 3200) mm, a masa wlewka wynosi 1,5 ~ 3 t;specyfikacje wlewków w dużych zakładach przetwórstwa miedzi. Ogólnie rzecz biorąc, jest to (150 ~ 250) mm x (630 ~ 1250) mm x (2400 ~ 8000) mm, a masa wlewka wynosi 4,5 ~ 20 t.
Podczas walcowania na gorąco temperatura powierzchni walca gwałtownie wzrasta w momencie styku walca z walcowanym przedmiotem o wysokiej temperaturze.Powtarzająca się rozszerzalność cieplna i skurcz na zimno powoduje powstawanie pęknięć i pęknięć na powierzchni walca.Dlatego podczas walcowania na gorąco należy przeprowadzić chłodzenie i smarowanie.Jako medium chłodząco-smarujące stosuje się zazwyczaj wodę lub emulsję o niższym stężeniu.Całkowita wydajność walcowania na gorąco wynosi zazwyczaj 90% do 95%.Grubość taśmy walcowanej na gorąco wynosi zazwyczaj od 9 do 16 mm.Frezowanie powierzchni taśmy po walcowaniu na gorąco może usunąć powierzchniowe warstwy tlenków, wtrącenia zgorzeliny i inne defekty powierzchni powstałe podczas odlewania, nagrzewania i walcowania na gorąco.W zależności od stopnia uszkodzenia powierzchni taśmy walcowanej na gorąco i potrzeb procesu, grubość frezowania każdej strony wynosi od 0,25 do 0,5 mm.
Walcarki gorące to na ogół walcarki nawrotne o dwóch lub czterech wysokościach.Wraz z powiększaniem wlewka i ciągłym wydłużaniem długości taśmy, poziom kontroli i funkcjonalność walcarki gorącej wykazują tendencję do ciągłego doskonalenia i udoskonalania, na przykład poprzez zastosowanie automatycznej kontroli grubości, hydraulicznych rolek gnących, przednich i tylnych walce pionowe, tylko walce chłodzące bez chłodzenia Urządzenie do walcowania, kontrola korony walca TP (Taper Pis-ton Roll), hartowanie online (hartowanie) po walcowaniu, zwijanie online i inne technologie poprawiające jednorodność struktury i właściwości taśmy oraz uzyskując lepsze płyta.
Technologia odlewania
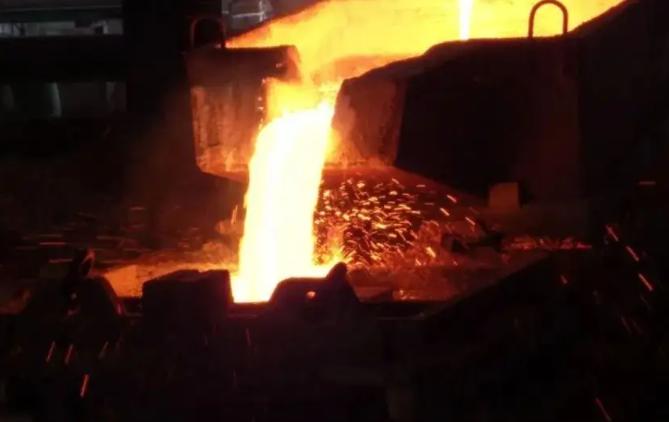
Odlewanie miedzi i stopów miedzi ogólnie dzieli się na: odlewanie półciągłe pionowe, odlewanie ciągłe pionowe, odlewanie ciągłe poziome, odlewanie ciągłe od góry i inne technologie odlewania.
A. Odlewanie półciągłe w pionie
Pionowe odlewanie półciągłe charakteryzuje się prostym wyposażeniem i elastyczną produkcją i nadaje się do odlewania różnych okrągłych i płaskich wlewków z miedzi i stopów miedzi.Tryb transmisji pionowej półciągłej maszyny odlewniczej dzieli się na hydrauliczny, śrubowy i linowy.Ponieważ przekładnia hydrauliczna jest stosunkowo stabilna, była częściej używana.W zależności od potrzeb krystalizator można wibrować z różną amplitudą i częstotliwością.Obecnie metoda odlewania półciągłego jest szeroko stosowana w produkcji wlewków miedzi i stopów miedzi.
B. Pionowe pełne odlewanie ciągłe
Pionowe, w pełni ciągłe odlewanie charakteryzuje się dużą wydajnością i wysoką wydajnością (około 98%), nadaje się do ciągłej produkcji wlewków na dużą skalę o jednej odmianie i specyfikacji i staje się jedną z głównych metod selekcji topienia i odlewania proces na nowoczesnych, wielkoskalowych liniach do produkcji taśm miedzianych.Pionowa, w pełni ciągła forma odlewnicza wykorzystuje bezdotykową, automatyczną kontrolę poziomu cieczy laserowej.W maszynie odlewniczej stosuje się zazwyczaj mocowanie hydrauliczne, przekładnię mechaniczną, cięcie i zbieranie wiórów na sucho w trybie on-line, automatyczne znakowanie i przechylanie wlewka.Struktura jest złożona, a stopień automatyzacji wysoki.
C. Odlewanie ciągłe w poziomie
Poziome odlewanie ciągłe może wytwarzać kęsy i kęsy drutu.
Poziome odlewanie ciągłe taśmy umożliwia produkcję taśm z miedzi i stopów miedzi o grubości 14-20 mm.Taśmy w tym zakresie grubości można bezpośrednio walcować na zimno bez walcowania na gorąco, dlatego często wykorzystuje się je do produkcji stopów trudnych do walcowania na gorąco (np. cyna, brąz fosforowy, mosiądz ołowiowy itp.), można z nich również wytwarzać mosiądz, taśma miedzioniklowa i niskostopowa miedź.W zależności od szerokości taśmy odlewniczej, w poziomym odlewaniu ciągłym można jednocześnie odlewać od 1 do 4 taśm.Powszechnie stosowane poziome maszyny do odlewania ciągłego mogą odlewać jednocześnie dwie taśmy, każda o szerokości mniejszej niż 450 mm, lub odlewać jedną taśmę o szerokości taśmy 650-900 mm.Pozioma taśma do ciągłego odlewania zazwyczaj przyjmuje proces odlewania typu pull-stop-reverse push, a na powierzchni występują okresowe linie krystalizacji, które zasadniczo należy wyeliminować przez frezowanie.Istnieją krajowe przykłady taśm miedzianych o dużej powierzchni, które można wytwarzać poprzez ciągnienie i odlewanie kęsów taśm bez frezowania.
Poziome ciągłe odlewanie kęsów rur, prętów i drutu umożliwia jednoczesne odlewanie od 1 do 20 wlewków, według różnych stopów i specyfikacji.Generalnie średnica pręta lub półwyrobu z drutu wynosi od 6 do 400 mm, a zewnętrzna średnica półwyrobu rury wynosi od 25 do 300 mm.Grubość ścianki wynosi 5-50 mm, a długość boku wlewka 20-300 mm.Zaletami metody poziomego odlewania ciągłego jest to, że proces jest krótki, koszt produkcji jest niski, a wydajność produkcji wysoka.Jednocześnie jest to również niezbędna metoda produkcji niektórych materiałów stopowych o słabej podatności na obróbkę na gorąco.Ostatnio jest to główna metoda wytwarzania kęsów z powszechnie stosowanych wyrobów z miedzi, takich jak taśmy z brązu cynowo-fosforowego, taśmy ze stopu cynku i niklu oraz rury klimatyzacyjne z miedzi odtlenionej fosforem.metody produkcji.
Wadami metody poziomego odlewania ciągłego są: odpowiednie odmiany stopów są stosunkowo proste, zużycie materiału grafitowego w wewnętrznej tulei formy jest stosunkowo duże, a jednorodność struktury krystalicznej przekroju wlewka nie jest łatwe do kontrolowania.Dolna część wlewka jest stale chłodzona pod wpływem grawitacji, która znajduje się blisko wewnętrznej ściany formy, a ziarna są drobniejsze;górna część wynika z powstawania szczelin powietrznych i wysokiej temperatury topnienia, co powoduje opóźnienie w krzepnięciu wlewka, co spowalnia szybkość chłodzenia i powoduje histerezę krzepnięcia wlewka.Struktura krystaliczna jest stosunkowo gruba, co jest szczególnie widoczne w przypadku wlewków o dużych rozmiarach.Mając na uwadze powyższe mankamenty, obecnie opracowywana jest metoda odlewania przy zginaniu pionowym za pomocą kęsów.Niemiecka firma użyła urządzenia do ciągłego odlewania zginanego pionowo do odlewania próbnego pasków brązu cynowego (16–18) mm × 680 mm, takiego jak DHP i CuSn6, z prędkością 600 mm/min.
D. Ciągłe rzucanie w górę
Odlewanie ciągłe w górę to technologia odlewania, która szybko rozwinęła się w ciągu ostatnich 20–30 lat i jest szeroko stosowana w produkcji kęsów drutu na walcówkę z jasnej miedzi.Wykorzystuje zasadę odlewania próżniowego i wykorzystuje technologię stop-pull, aby realizować ciągłe odlewanie wielogłowicowe.Charakteryzuje się prostym sprzętem, niewielką inwestycją, mniejszą utratą metalu i procedurami o niskim zanieczyszczeniu środowiska.Odlewanie ciągłe w górę jest ogólnie odpowiednie do produkcji kęsów drutu z miedzi czerwonej i miedzi beztlenowej.Nowym osiągnięciem opracowanym w ostatnich latach jest jego popularyzacja i zastosowanie w półwyrobach rurowych o dużej średnicy, mosiądzu i miedzioniklu.Obecnie opracowano instalację do ciągłego odlewania od góry o wydajności 5000 ton rocznie i średnicy ponad Φ100 mm;Wyprodukowano binarne kęsy z trójskładnikowego drutu ze zwykłego mosiądzu i cynkowo-białej miedzi, a wydajność kęsów z drutu może osiągnąć ponad 90%.
E. Inne techniki odlewnicze
Technologia kęsów do ciągłego odlewania jest w fazie rozwoju.Eliminuje defekty, takie jak ślady powstałe na zewnętrznej powierzchni kęsa w wyniku procesu ciągłego odlewania w górę, a jakość powierzchni jest doskonała.A ze względu na prawie kierunkowe właściwości krzepnięcia, struktura wewnętrzna jest bardziej jednolita i czysta, więc wydajność produktu jest również lepsza.Technologia produkcji kęsów drutu miedzianego do ciągłego odlewania taśmowego jest szeroko stosowana na dużych liniach produkcyjnych o masie powyżej 3 ton.Pole przekroju wlewka wynosi na ogół ponad 2000 mm2, a za nim znajduje się walcarka ciągła o wysokiej wydajności produkcyjnej.
Odlewanie elektromagnetyczne próbowano w moim kraju już w latach 70. XX wieku, ale nie wdrożono jeszcze produkcji przemysłowej.W ostatnich latach technologia odlewania elektromagnetycznego poczyniła ogromne postępy.Obecnie z powodzeniem odlewane są wlewki z miedzi beztlenowej o średnicy Φ200 mm o gładkiej powierzchni.Jednocześnie mieszanie pola elektromagnetycznego na stopiony materiał może sprzyjać usuwaniu gazów spalinowych i żużla, dzięki czemu można uzyskać miedź beztlenową o zawartości tlenu poniżej 0,001%.
Kierunkiem nowej technologii odlewania stopów miedzi jest poprawa struktury formy poprzez kierunkowe krzepnięcie, szybkie krzepnięcie, formowanie półstałe, mieszanie elektromagnetyczne, obróbkę metamorficzną, automatyczną kontrolę poziomu cieczy i inne środki techniczne zgodnie z teorią krzepnięcia., zagęszczanie, oczyszczanie i realizowanie ciągłej pracy oraz formowania bliskiego końca.
W dłuższej perspektywie odlewanie miedzi i stopów miedzi będzie stanowić połączenie technologii odlewania półciągłego i technologii odlewania pełnego ciągłego, a udział technologii odlewania ciągłego będzie stale rósł.
Technologia walcowania na zimno
Zgodnie ze specyfikacją taśmy walcowanej i procesem walcowania, walcowanie na zimno dzieli się na walcowanie wykańczające, walcowanie pośrednie i walcowanie wykańczające.Proces walcowania na zimno odlanej taśmy o grubości od 14 do 16 mm i walcowanej na gorąco kęsa o grubości od około 5 do 16 mm do 2 do 6 mm nazywa się wykwitaniem, a procesem ciągłego zmniejszania grubości walcowany element nazywany jest walcowaniem pośrednim.końcowe walcowanie na zimno w celu spełnienia wymagań gotowego produktu nazywa się walcowaniem wykańczającym.
Proces walcowania na zimno musi kontrolować system redukcji (całkowita szybkość przetwarzania, szybkość przetwarzania przejścia i szybkość przetwarzania gotowego produktu) zgodnie z różnymi stopami, specyfikacjami walcowania i wymaganiami dotyczącymi wydajności produktu gotowego, rozsądnie wybierać i dostosowywać kształt walca oraz rozsądnie wybierać smarowanie metoda i smar.Pomiar i regulacja napięcia.
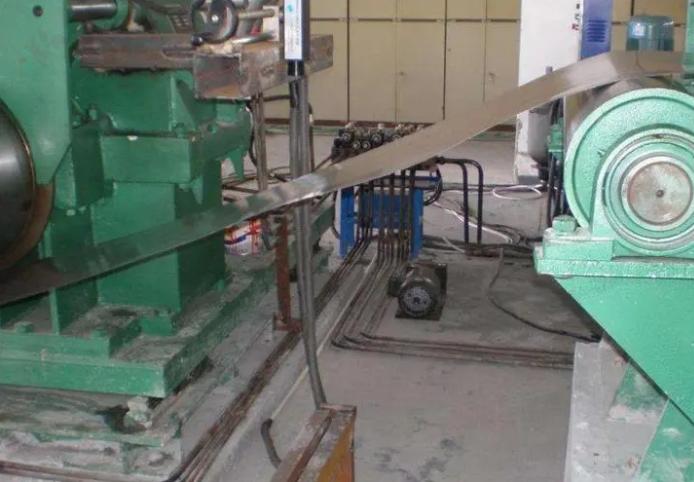
W walcowniach zimnych na ogół stosuje się walcarki nawrotne o czterech lub wielu wysokościach.Nowoczesne walcownie na zimno zazwyczaj wykorzystują szereg technologii, takich jak hydrauliczne gięcie walców dodatnich i ujemnych, automatyczna kontrola grubości, nacisku i naprężenia, ruch osiowy rolek, segmentowe chłodzenie rolek, automatyczna kontrola kształtu blachy i automatyczne wyrównywanie walcowanych elementów , dzięki czemu można poprawić dokładność paska.Do 0,25±0,005 mm i w granicach 5I kształtu płytki.
Trend rozwojowy technologii walcowania na zimno znajduje odzwierciedlenie w rozwoju i zastosowaniu wysokoprecyzyjnych walcarek wielowalcowych, wyższych prędkościach walcowania, dokładniejszej kontroli grubości i kształtu taśmy oraz technologii pomocniczych, takich jak chłodzenie, smarowanie, zwijanie, centrowanie i szybkie walcowanie zmiana.udoskonalenie itp.
Sprzęt produkcyjny - piec dzwonowy
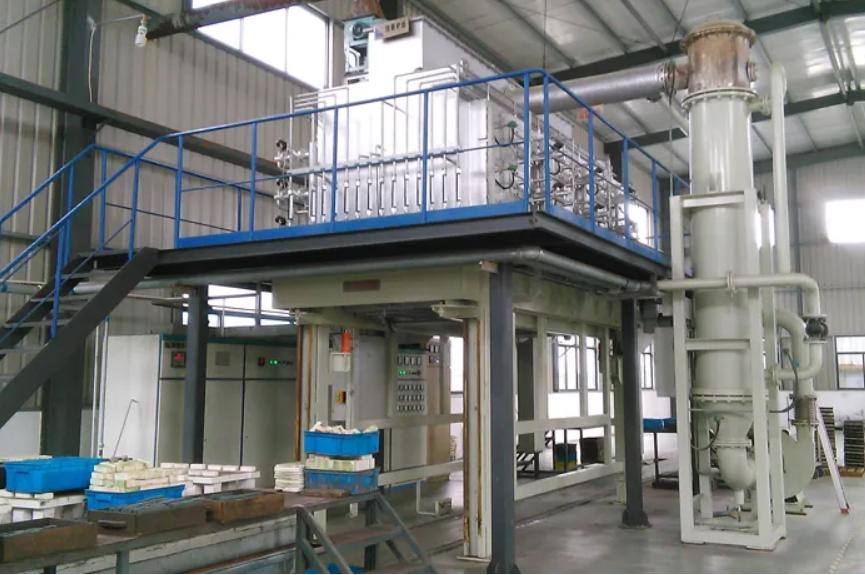
Piece kielichowe i piece przenoszące są powszechnie stosowane w produkcji przemysłowej i testach pilotażowych.Ogólnie rzecz biorąc, moc jest duża, a zużycie energii jest duże.W przypadku przedsiębiorstw przemysłowych materiałem pieca do podnoszenia Luoyang Sigma jest włókno ceramiczne, które ma dobry efekt oszczędzania energii, niskie zużycie energii i niskie zużycie energii.Oszczędzaj energię elektryczną i czas, co jest korzystne dla zwiększenia produkcji.
Dwadzieścia pięć lat temu niemieckie marki BRANDS i Philips, wiodąca firma w branży produkcji ferrytów, wspólnie opracowały nową maszynę do spiekania.Rozwój tego sprzętu zaspokaja specjalne potrzeby przemysłu ferrytowego.W trakcie tego procesu piec dzwonowy BRANDS jest stale unowocześniany.
Zwraca uwagę na potrzeby znanych na całym świecie firm takich jak Philips, Siemens, TDK, FDK itp., które również czerpią ogromne korzyści z wysokiej jakości sprzętu MAREK.
Ze względu na wysoką stabilność produktów wytwarzanych przez piece dzwonowe, piece dzwonowe stały się czołowymi firmami w branży profesjonalnej produkcji ferrytu.Dwadzieścia pięć lat temu pierwszy piec marki BRANDS nadal wytwarza wysokiej jakości produkty dla firmy Philips.
Główną cechą pieca do spiekania oferowanego przez piec dzwonowy jest jego wysoka wydajność.Jego inteligentny system sterowania i inne wyposażenie tworzą kompletną jednostkę funkcjonalną, która może w pełni sprostać niemal najnowocześniejszym wymaganiom przemysłu ferrytycznego.
Klienci pieców kielichowych mogą programować i przechowywać dowolny profil temperatury/atmosfery wymagany do wytwarzania produktów wysokiej jakości.Ponadto klienci mogą wyprodukować na czas także dowolne inne produkty, zgodnie z rzeczywistymi potrzebami, skracając w ten sposób czas realizacji i redukując koszty.Sprzęt do spiekania musi mieć dobrą zdolność regulacji, aby wytwarzać różnorodne produkty i stale dostosowywać się do potrzeb rynku.Oznacza to, że odpowiadające im produkty muszą być produkowane według indywidualnych potrzeb klienta.
Dobry producent ferrytu może wyprodukować ponad 1000 różnych magnesów, aby zaspokoić specjalne potrzeby klientów.Wymagają one możliwości powtarzania procesu spiekania z dużą precyzją.Systemy pieców kielichowych stały się standardowymi piecami dla wszystkich producentów ferrytu.
W przemyśle ferrytowym piece te są stosowane głównie w przypadku ferrytu o niskim zużyciu energii i wysokiej wartości μ, szczególnie w przemyśle komunikacyjnym.Bez pieca dzwonowego nie da się wyprodukować wysokiej jakości rdzeni.
Piec dzwonowy wymaga tylko kilku operatorów podczas spiekania, załadunek i rozładunek można zakończyć w ciągu dnia, a spiekanie można zakończyć w nocy, umożliwiając maksymalne wykorzystanie energii elektrycznej, co jest bardzo praktyczne w dzisiejszej sytuacji niedoborów energii.Piece jarzeniowe wytwarzają produkty wysokiej jakości, a wszystkie dodatkowe inwestycje szybko się zwracają dzięki produktom wysokiej jakości.Sterowanie temperaturą i atmosferą, konstrukcja pieca oraz kontrola przepływu powietrza w piecu są doskonale zintegrowane, aby zapewnić równomierne ogrzewanie i chłodzenie produktu.Kontrola atmosfery pieca podczas chłodzenia jest bezpośrednio związana z temperaturą pieca i może zagwarantować zawartość tlenu na poziomie 0,005% lub nawet niższą.A to są rzeczy, których nie potrafi nasza konkurencja.
Dzięki kompletnemu systemowi programowania alfanumerycznego można łatwo odtworzyć długie procesy spiekania, zapewniając w ten sposób jakość produktu.Sprzedaż produktu jest także odzwierciedleniem jego jakości.
Technologia obróbki cieplnej
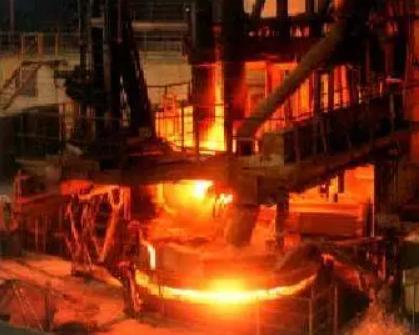
Kilka wlewków stopowych (pasków) poddawanych silnej segregacji dendrytów lub naprężeniom odlewniczym, takich jak brąz cynowo-fosforowy, wymaga specjalnego wyżarzania homogenizującego, które zwykle przeprowadza się w piecu jarzeniowym.Temperatura wyżarzania homogenizującego wynosi na ogół od 600 do 750°C.
Obecnie większość wyżarzania pośredniego (wyżarzanie rekrystalizacyjne) i wyżarzania końcowego (wyżarzanie w celu kontrolowania stanu i wydajności produktu) taśm ze stopów miedzi jest wyżarzana na połysk przez ochronę gazową.Rodzaje pieców obejmują piec kielichowy, piec z poduszką powietrzną, piec z trakcją pionową itp. Wyżarzanie utleniające jest wycofywane.
Trend rozwojowy technologii obróbki cieplnej znajduje odzwierciedlenie w obróbce metodą walcowania na gorąco materiałów stopowych wzmocnionych wydzieleniowo, a następnie w technologii obróbki cieplnej odkształcającej, ciągłym wyżarzaniu jasnym i wyżarzaniu rozciągającym w atmosferze ochronnej.
Hartowanie — starzenie się obróbki cieplnej stosuje się głównie do ulepszania cieplnego wzmacniania stopów miedzi.Poprzez obróbkę cieplną produkt zmienia swoją mikrostrukturę i uzyskuje wymagane specjalne właściwości.Wraz z rozwojem stopów o wysokiej wytrzymałości i wysokiej przewodności, proces obróbki cieplnej przez hartowanie i starzenie będzie coraz częściej stosowany.Sprzęt do obróbki starzenia jest mniej więcej taki sam jak sprzęt do wyżarzania.
Technologia wytłaczania
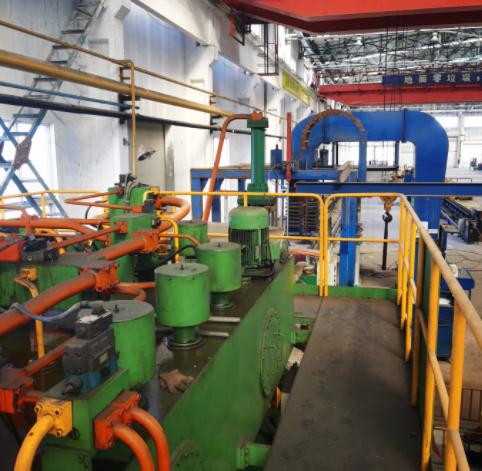
Wytłaczanie to dojrzała i zaawansowana metoda produkcji rur, prętów, profili i dostarczania kęsów z miedzi i stopów miedzi.Zmieniając matrycę lub stosując metodę wytłaczania perforacyjnego, można bezpośrednio wytłaczać różne odmiany stopów i różne kształty przekrojów.Poprzez wytłaczanie odlewana struktura wlewka zmienia się w przetworzoną strukturę, a wytłaczany kęs rurowy i kęs prętowy mają wysoką dokładność wymiarową, a struktura jest cienka i jednolita.Metoda wytłaczania jest metodą produkcji powszechnie stosowaną przez krajowych i zagranicznych producentów rur i prętów miedzianych.
Kucie stopów miedzi jest wykonywane głównie przez producentów maszyn w moim kraju, obejmując głównie kucie swobodne i kucie matrycowe, takie jak duże koła zębate, przekładnie ślimakowe, ślimaki, pierścienie zębate synchronizatorów samochodowych itp.
Metodę wytłaczania można podzielić na trzy typy: wytłaczanie do przodu, wytłaczanie odwrotne i wytłaczanie specjalne.Wśród nich znajduje się wiele zastosowań wytłaczania w przód, wytłaczanie odwrotne stosowane jest w produkcji małych i średnich prętów i drutów, a w produkcji specjalnej stosuje się wytłaczanie specjalne.
Przy wytłaczaniu, kierując się właściwościami stopu, wymaganiami technicznymi wytłaczanych wyrobów oraz wydajnością i konstrukcją wytłaczarki, należy rozsądnie dobrać rodzaj, wielkość i współczynnik wytłaczania wlewka, tak aby stopień odkształcenia był nie mniej niż 85%.Temperatura wytłaczania i prędkość wytłaczania są podstawowymi parametrami procesu wytłaczania, a rozsądny zakres temperatur wytłaczania należy określić na podstawie wykresu plastyczności i diagramu fazowego metalu.W przypadku miedzi i stopów miedzi temperatura wytłaczania wynosi na ogół od 570 do 950°C, a temperatura wytłaczania miedzi sięga nawet od 1000 do 1050°C.W porównaniu z temperaturą ogrzewania cylindra wytłaczającego wynoszącą od 400 do 450 ° C, różnica temperatur między nimi jest stosunkowo wysoka.Jeżeli prędkość wytłaczania będzie zbyt mała, temperatura powierzchni wlewka będzie zbyt szybko spadać, co spowoduje wzrost nierównomierności przepływu metalu, co doprowadzi do wzrostu obciążenia wyciskania, a nawet spowoduje zjawisko wytaczania .Dlatego miedź i stopy miedzi na ogół stosują stosunkowo szybkie wytłaczanie, prędkość wytłaczania może osiągnąć ponad 50 mm/s.
W przypadku wytłaczania miedzi i stopów miedzi często stosuje się wytłaczanie złuszczające w celu usunięcia defektów powierzchni wlewka, a grubość łuszczenia wynosi 1-2 m.Zwykle na wyjściu kęsa wytłaczanego stosuje się uszczelnienie wodne, dzięki czemu produkt można schłodzić w zbiorniku wody po wytłaczaniu, a powierzchnia produktu nie ulega utlenieniu, a późniejszą obróbkę na zimno można przeprowadzić bez trawienia.Zwykle wykorzystuje wytłaczarkę wielkotonażową z synchronicznym urządzeniem odbierającym do wytłaczania zwojów rur lub drutu o pojedynczej masie większej niż 500 kg, aby skutecznie poprawić wydajność produkcji i kompleksową wydajność kolejnej sekwencji.Obecnie do produkcji rur z miedzi i stopów miedzi wykorzystuje się głównie poziome hydrauliczne wytłaczarki do przodu z niezależnym systemem perforacji (podwójnego działania) i bezpośrednią przekładnią pompy olejowej, a do produkcji prętów wykorzystuje się głównie niezależny system perforacji (pojedynczego działania) i bezpośrednia skrzynia biegów pompy olejowej.Pozioma hydrauliczna wytłaczarka do przodu lub do tyłu.Powszechnie stosowane specyfikacje wytłaczarek to 8-50 MN, a obecnie jest ono zwykle produkowane w wytłaczarkach o dużym tonażu powyżej 40 MN w celu zwiększenia pojedynczego ciężaru wlewka, poprawiając w ten sposób wydajność produkcji i wydajność.
Nowoczesne poziome wytłaczarki hydrauliczne są konstrukcyjnie wyposażone we wstępnie naprężoną integralną ramę, prowadnicę i wspornik cylindra wytłaczającego „X”, wbudowany system perforacji, wewnętrzne chłodzenie igły perforacyjnej, zestaw matryc ślizgowych lub obrotowych oraz urządzenie do szybkiej wymiany matryc, bezpośrednią pompę olejową o dużej mocy i zmiennej zmiennej napęd, zintegrowany zawór logiczny, sterowanie PLC i inne zaawansowane technologie, sprzęt ma wysoką precyzję, zwartą konstrukcję, stabilną pracę, bezpieczne blokowanie i łatwe do zrealizowania sterowanie programem.Technologia ciągłego wytłaczania (Conform) poczyniła pewne postępy w ciągu ostatnich dziesięciu lat, szczególnie w przypadku produkcji prętów o specjalnym kształcie, takich jak przewody lokomotyw elektrycznych, co jest bardzo obiecujące.W ostatnich dziesięcioleciach nowa technologia wytłaczania szybko się rozwinęła, a trend rozwojowy technologii wytłaczania jest następujący: (1) Sprzęt do wytłaczania.Siła wytłaczania prasy do wytłaczania będzie rozwijać się w większym kierunku, a prasa do wytłaczania o masie ponad 30 MN stanie się głównym korpusem, a automatyzacja linii produkcyjnej prasy do wytłaczania będzie w dalszym ciągu doskonalona.Nowoczesne maszyny do wytłaczania całkowicie przyjęły sterowanie programami komputerowymi i programowalne sterowanie logiczne, dzięki czemu znacznie poprawia się wydajność produkcji, znacznie zmniejsza się liczba operatorów, a nawet możliwa jest automatyczna, bezobsługowa obsługa linii produkcyjnych do wytłaczania.
Stale ulepszana i udoskonalana jest także konstrukcja korpusu wytłaczarki.W ostatnich latach w niektórych wytłaczarkach poziomych zastosowano wstępnie naprężoną ramę, aby zapewnić stabilność całej konstrukcji.Nowoczesna wytłaczarka realizuje metody wytłaczania do przodu i do tyłu.Wytłaczarka wyposażona jest w dwa wały wytłaczające (główny wał wytłaczający i wał matrycowy).Podczas wytłaczania cylinder wytłaczający porusza się wraz z wałem głównym.W tym momencie produkt jest Kierunek wypływu jest zgodny z kierunkiem ruchu wału głównego i przeciwny do względnego kierunku ruchu osi matrycy.Podstawa matrycy wytłaczarki przyjmuje również konfigurację wielu stacji, co nie tylko ułatwia wymianę matrycy, ale także poprawia wydajność produkcji.Nowoczesne wytłaczarki wykorzystują urządzenie do regulacji odchylenia lasera, które zapewnia skuteczne dane o stanie linii środkowej wytłaczania, co jest wygodne do terminowej i szybkiej regulacji.Prasa hydrauliczna z napędem bezpośrednim z pompą wysokociśnieniową, wykorzystująca olej jako czynnik roboczy, całkowicie zastąpiła prasę hydrauliczną.Narzędzia do wytłaczania są również stale aktualizowane wraz z rozwojem technologii wytłaczania.Szeroko promowano wewnętrzną igłę do przekłuwania chłodzoną wodą, a igła do przekłuwania i toczenia o zmiennym przekroju poprzecznym znacznie poprawia efekt smarowania.Coraz szerzej stosowane są formy ceramiczne i formy ze stali stopowej o dłuższej żywotności i wyższej jakości powierzchni.
Narzędzia do wytłaczania są również stale aktualizowane wraz z rozwojem technologii wytłaczania.Szeroko promowano wewnętrzną igłę do przekłuwania chłodzoną wodą, a igła do przekłuwania i toczenia o zmiennym przekroju poprzecznym znacznie poprawia efekt smarowania.Coraz popularniejsze jest stosowanie form ceramicznych i ze stali stopowych o dłuższej żywotności i wyższej jakości powierzchni.(2) Proces produkcji metodą wytłaczania.Odmiany i specyfikacje wyrobów wytłaczanych stale się poszerzają.Wytłaczanie ultraprecyzyjnych rur, prętów, profili i bardzo dużych profili o małych przekrojach zapewnia jakość wyglądu produktów, zmniejsza wady wewnętrzne produktów, zmniejsza straty geometryczne i dodatkowo promuje metody wytłaczania, takie jak jednolita wydajność wytłaczanych produkty.Szeroko stosowana jest również nowoczesna technologia wytłaczania odwrotnego.W przypadku metali łatwo utlenionych stosuje się wytłaczanie z uszczelnieniem wodnym, które może zmniejszyć zanieczyszczenie spowodowane trawieniem, zmniejszyć straty metalu i poprawić jakość powierzchni produktów.W przypadku produktów wytłaczanych, które wymagają hartowania, wystarczy kontrolować odpowiednią temperaturę.Metoda wytłaczania uszczelnienia wodnego może osiągnąć cel, skutecznie skrócić cykl produkcyjny i zaoszczędzić energię.
Wraz z ciągłym doskonaleniem wydajności wytłaczarki i technologii wytłaczania, stopniowo stosowano nowoczesne technologie wytłaczania, takie jak wytłaczanie izotermiczne, wytłaczanie z matrycą chłodzącą, wytłaczanie z dużą prędkością i inne technologie wytłaczania do przodu, wytłaczanie odwrotne, wytłaczanie hydrostatyczne Praktyczne zastosowanie technologii ciągłego wytłaczania prasowania i Conform, zastosowanie technologii wytłaczania proszków i warstwowego wytłaczania kompozytów niskotemperaturowych materiałów nadprzewodnikowych, rozwój nowych metod, takich jak wytłaczanie metali półstałych i wytłaczanie wieloformatowe, rozwój małych precyzyjnych części Technologia formowania przez wytłaczanie na zimno, itp., zostały szybko opracowane i powszechnie stosowane.
Spektrometr
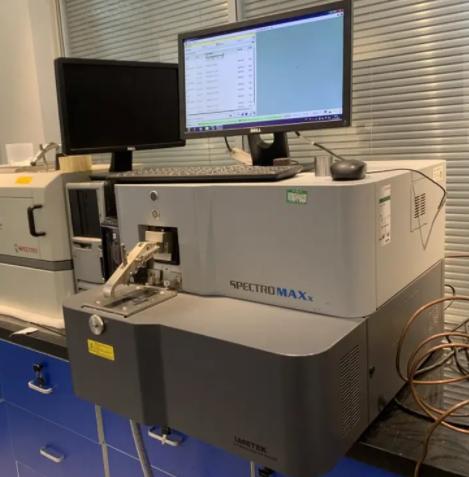
Spektroskop to instrument naukowy, który rozkłada światło o złożonym składzie na linie widmowe.Siedmiokolorowe światło słoneczne to część, którą można rozróżnić gołym okiem (światło widzialne), ale jeśli światło słoneczne zostanie rozłożone przez spektrometr i uporządkowane według długości fali, światło widzialne zajmuje tylko niewielki zakres widma, a reszta to widma, których nie można rozróżnić gołym okiem, takie jak promienie podczerwone, mikrofale, promienie UV, promienie rentgenowskie itp. Informacje optyczne są przechwytywane przez spektrometr, wywoływane na kliszy fotograficznej lub wyświetlane i analizowane na skomputeryzowanym automatycznym wyświetlaczu przyrząd numeryczny, aby wykryć, jakie elementy znajdują się w wyrobie.Technologia ta jest szeroko stosowana w wykrywaniu zanieczyszczeń powietrza, wody, higieny żywności, przemyśle metalowym itp.
Spektrometr, znany również jako spektrometr, jest powszechnie znany jako spektrometr z bezpośrednim odczytem.Urządzenie mierzące intensywność linii widmowych przy różnych długościach fal za pomocą fotodetektorów, takich jak fotopowielacze.Składa się ze szczeliny wejściowej, systemu dyspersyjnego, systemu obrazującego i jednej lub więcej szczelin wyjściowych.Promieniowanie elektromagnetyczne źródła promieniowania jest rozdzielane na wymaganą długość fali lub obszar długości fali przez element dyspersyjny, a natężenie jest mierzone przy wybranej długości fali (lub skanowaniu określonego pasma).Istnieją dwa rodzaje monochromatorów i polichromatorów.
Instrument testowy-miernik przewodności
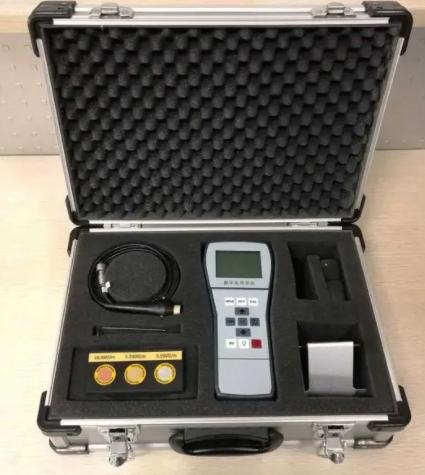
Cyfrowy ręczny tester przewodności metalu (miernik przewodności) FD-101 wykorzystuje zasadę wykrywania prądów wirowych i został specjalnie zaprojektowany zgodnie z wymaganiami przewodnictwa przemysłu elektrycznego.Spełnia standardy testowania przemysłu metalowego pod względem funkcjonalności i dokładności.
1. Miernik przewodności wiroprądowej FD-101 posiada trzy unikalne cechy:
1) Jedyny chiński miernik przewodności, który przeszedł weryfikację Instytutu Materiałów Lotniczych;
2) Jedyny chiński miernik przewodności, który może zaspokoić potrzeby firm z branży lotniczej;
3) Jedyny chiński miernik przewodności eksportowany do wielu krajów.
2. Wprowadzenie do funkcji produktu:
1) Duży zakres pomiarowy: 6,9% IACS-110% IACS (4,0 MS/m-64 MS/m), który spełnia test przewodności wszystkich metali nieżelaznych.
2) Inteligentna kalibracja: szybka i dokładna, całkowicie unikająca błędów ręcznej kalibracji.
3) Przyrząd ma dobrą kompensację temperatury: odczyt jest automatycznie kompensowany do wartości przy 20°C, a na korektę nie ma wpływu błąd ludzki.
4) Dobra stabilność: to Twój osobisty strażnik kontroli jakości.
5) Humanizowane inteligentne oprogramowanie: zapewnia wygodny interfejs wykrywania oraz zaawansowane funkcje przetwarzania i gromadzenia danych.
6) Wygodna obsługa: zakład produkcyjny i laboratorium można wykorzystać wszędzie, zdobywając przychylność większości użytkowników.
7) Samodzielna wymiana sond: Każdy host może być wyposażony w wiele sond, a użytkownicy mogą je wymieniać w dowolnym momencie.
8) Rozdzielczość numeryczna: 0,1% IACS (MS/m)
9) Interfejs pomiarowy wyświetla jednocześnie wartości pomiarowe w dwóch jednostkach %IACS i MS/m.
10) Posiada funkcję przechowywania danych pomiarowych.
Twardościomierz
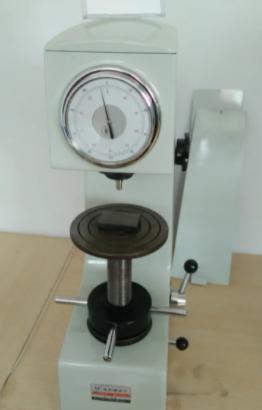
Przyrząd charakteryzuje się unikalną i precyzyjną konstrukcją pod względem mechaniki, optyki i źródła światła, dzięki czemu obrazowanie wgłębień jest wyraźniejsze, a pomiar dokładniejszy.W pomiarze mogą brać udział zarówno obiektywy o powiększeniu 20x, jak i 40x, co zwiększa zakres pomiarowy i rozszerza zastosowanie.Przyrząd jest wyposażony w cyfrowy mikroskop pomiarowy, który może wyświetlać na ekranie cieczowym metodę badania, siłę testową, długość wcięcia, wartość twardości, czas utrzymywania siły testowej, czasy pomiaru itp. oraz posiada gwintowany interfejs, który można podłączyć do aparatu cyfrowego i kamery CCD.Ma pewną reprezentatywność w krajowych produktach głowy.
Testowanie detektora rezystancji przyrządu
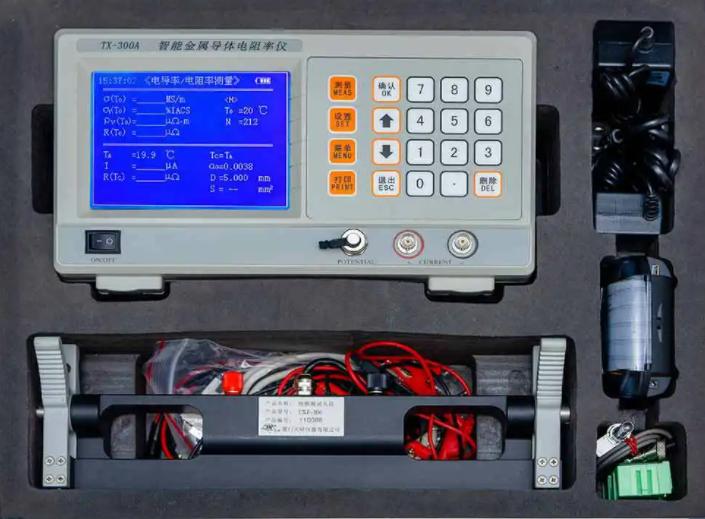
Przyrząd do pomiaru rezystywności drutu metalowego jest wysokowydajnym przyrządem do testowania takich parametrów, jak drut, rezystywność pręta i przewodność elektryczna.Jego działanie jest w pełni zgodne z odpowiednimi wymaganiami technicznymi zawartymi w GB/T3048.2 i GB/T3048.4.Szeroko stosowane w metalurgii, energetyce elektrycznej, drutach i kablach, urządzeniach elektrycznych, szkołach wyższych i uniwersytetach, jednostkach naukowo-badawczych i innych gałęziach przemysłu.
Główne cechy instrumentu:
(1) integruje zaawansowaną technologię elektroniczną, technologię jednoukładową i technologię automatycznego wykrywania, z silną funkcją automatyzacji i prostą obsługą;
(2) Wystarczy nacisnąć klawisz raz, wszystkie zmierzone wartości można uzyskać bez żadnych obliczeń, co nadaje się do ciągłego, szybkiego i dokładnego wykrywania;
(3) Konstrukcja na baterie, mały rozmiar, łatwy do przenoszenia, odpowiedni do użytku w terenie;
(4) Duży ekran, duża czcionka, może wyświetlać jednocześnie rezystywność, przewodność, rezystancję i inne zmierzone wartości oraz temperaturę, prąd testowy, współczynnik kompensacji temperatury i inne parametry pomocnicze, bardzo intuicyjne;
(5) Jedna maszyna jest wielofunkcyjna i posiada 3 interfejsy pomiarowe, mianowicie interfejs pomiaru rezystywności i przewodności przewodu, kompleksowy interfejs pomiaru parametrów kabla i interfejs pomiaru rezystancji kabla DC (typ TX-300B);
(6) Każdy pomiar posiada funkcje automatycznego wyboru prądu stałego, automatycznej komutacji prądu, automatycznej korekcji punktu zerowego i automatycznej korekcji kompensacji temperatury, aby zapewnić dokładność każdej wartości pomiaru;
(7) Unikalny przenośny przyrząd testowy z czterema zaciskami nadaje się do szybkiego pomiaru różnych materiałów i różnych specyfikacji drutów lub prętów;
(8) Wbudowana pamięć danych, która może rejestrować i zapisywać 1000 zestawów danych pomiarowych i parametrów pomiarowych oraz łączyć się z górnym komputerem w celu wygenerowania pełnego raportu.